Flexographic printing (often abbreviated as flexo) has quietly become the backbone of global manufacturing, powering everything from cereal boxes to pharmaceutical labels. Accounting for over 40% of the global packaging print market (Statista, 2023) and valued at $168 billion, this dynamic printing method combines speed, versatility, and precision to meet the demands of today’s fast-paced consumer economy. But what exactly makes flexo printing a go-to solution for industries worldwide? Let’s dive into the mechanics, innovations, and economic drivers behind this transformative technology.
The Anatomy of Flexo Printing: Speed Meets Adaptability
At its core, flexographic printing employs flexible photopolymer plates mounted on rotating cylinders to transfer ink onto substrates. Unlike rigid printing plates used in offset or gravure methods, these elastomeric plates conform to uneven surfaces, enabling printing on materials as diverse as:
-
1.Corrugated cardboard
-
2.Thin plastic films (e.g., PET, BOPP)
-
3.Metallic foils for luxury packaging
-
4.Recyclable paper and compostable bioplastics
The process thrives in roll-to-roll (R2R) systems, where materials feed continuously from massive reels, passing through multiple print stations for layered color application, varnishing, or functional coatings (e.g., moisture barriers).
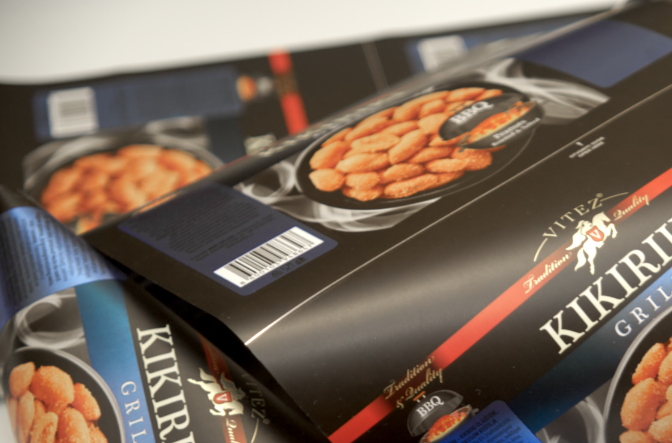
Why Industries Choose Flexo: 5 Unmatched Advantages
-
Material Agnosticism
Flexo works seamlessly across absorbent (paper) and non-absorbent (plastics) surfaces, outperforming digital printers in handling textured or heat-sensitive substrates.
-
Ink Versatility
From water-based inks for food-safe packaging (FDA-compliant) to UV-curable inks for scratch-resistant electronics labels, flexo adapts to regulatory and durability needs. Solvent-based inks dominate in outdoor applications (e.g., weather-resistant shipping tags).
-
Economies of Scale
A single flexo press can churn out 6,000+ linear feet of material per hour—6x faster than most digital printers—with minimal setup time for long runs. Cost per unit plummets for high-volume orders.
-
Sustainability Edge
Modern flexo systems reduce waste by 30% compared to gravure, thanks to precise anilox rollers that meter nano-thin ink layers. Water-based inks and energy-efficient LED-UV curing further align with ESG goals.
-
Hybrid Integration
Flexo presses now incorporate digital print units for variable data (e.g., QR codes) and embossing modules for tactile finishes, merging flexibility with specialty effects.
Behind the Scenes: Cutting-Edge Innovations
Recent breakthroughs are redefining flexo’s capabilities:
-
Laser-Engraved Anilox Rollers: Micro-engineered cells (1.5–8 BCM/in²) ensure ink transfer accuracy down to ±0.1 µm, eliminating blotching.
-
High-Resolution Plates: 3D-printed digital plates achieve 150–200 lpi resolution, rivaling offset print quality.
-
Smart Presses: AI-driven systems auto-adjust ink viscosity and registration in real-time, reducing manual checks by 70%.
Flexo vs. Digital vs. Offset: Strategic Trade-Offs
Factor |
Flexographic |
Digital |
Offset |
Cost Efficiency |
Best for >10,000 units |
Optimal for <5,000 units |
Mid-volume (5k–50k) |
Setup Time |
1–2 hours |
<15 minutes |
2–4 hours |
Material Range |
Broadest (plastics, foil) |
Limited to coated papers |
Paper-centric |
Customization |
Low (fixed designs) |
High (variable data) |
Moderate |
For brands like PepsiCo or Amazon, flexo remains irreplaceable for mass-producing identical packaging with metallics or spot varnishes—a feat still costly for digital alternatives.
Inside a Flexo Press: Machine Types Decoded
-
Central Impression (CI) Presses
-
Stack Presses
-
Inline Presses
-
Narrow-Web vs. Wide-Web
-
Narrow-web (≤20”): Labels, tags.
-
Wide-web (40”–80”): Wallpaper, bulk pouches.
The Future: Automation and Eco-Innovation
With 65% of converters investing in servo-driven presses (Smithers, 2024), flexo is entering an era of autonomous operation. Emerging trends include:
-
Bio-based Photopolymer Plates: Compostable plates to replace petroleum-derived analogs.
-
Nanographic Hybrids: Combining flexo’s speed with nanographic inkjet detail.
-
Blockchain Integration: Tracking ink usage and waste for carbon credit audits.
From supermarket shelves to SpaceX component labels, flexographic printing’s blend of speed and adaptability ensures its dominance in the 21st-century supply chain. As circular economy mandates tighten, expect flexo tech to lead the charge in sustainable, high-volume print solutions.
Ready to explore flexo for your packaging line? Dive into our Flexo Printing Machine selector tool or consult our engineers for a tailored ROI analysis.